You’ve arrived at this website, so chances are you already know the advantages that China manufacturing can offer your business. What you may not know is exactly how that process happens. Even if you understand how to shop for suppliers , the process of getting a product manufactured in China is often concealed in mystery.
Unless, of course, you read this article! The Kanary Team will take you step-by-step and teach you how to get your product manufactured in China, including the importance of detailed plans, managing samples, and supervising quality control.
Send Detailed, Specific Product Schematics
When you've landed on a supplier, the first thing you need to do is send them your product schematics. This will let the manufacturer know the specifics of your product, including preferred dimensions, material type, etc. Your product plans should be as detailed as possible since this is what the manufacturer will refer to when making your product.
If you know your product will be metal, don't list "metal" in your schematics. You need to be far more specific (for example, listing "aluminum" as your preferred material). If you have more information available, go a few steps further. For example, include the desired purity or grade of raw materials, the tensile strength of raw materials, or even your preferred density.
These specific details will be listed in your design files, such as the supplier preferred adobe design file, or whatever format file you and your supplier decide on. You need to triple and quadruple-check these files and proofs you plan to use. Once you give the supplier the go-ahead, it will be too late to make any revisions to the schematics.
Detailed Design Plans Hold Manufacturers Accountable
Providing highly detailed plans will help avoid accidents, mistakes, and misunderstandings between you and your supplier. However, it will also allow you to hold the supplier responsible if the product they make is not up to the standards listed in your design plans.
Not only should your plans be specific for referral, but you should also keep a record of all conversations between you and the supplier for the same reason. You can refer back to the details in the design plan as well as details in previous conversations.
If you have clear proof that you provided accurate design details that the supplier didn't follow, you'll have the ability to convince a supplier to correct the mistakes they have made (and at their own expense instead of yours).
Samples
After you have sent and confirmed product schematics with your supplier, you will want to order a sample before they start mass-producing your product. This is standard practice. If a supplier is hesitant or unwilling to provide a sample, this is an enormous red flag. It will be time to hit the brakes and shop for a new supplier.
Getting samples are incredibly important, as they allow you to confirm the following information before you begin large volume production:
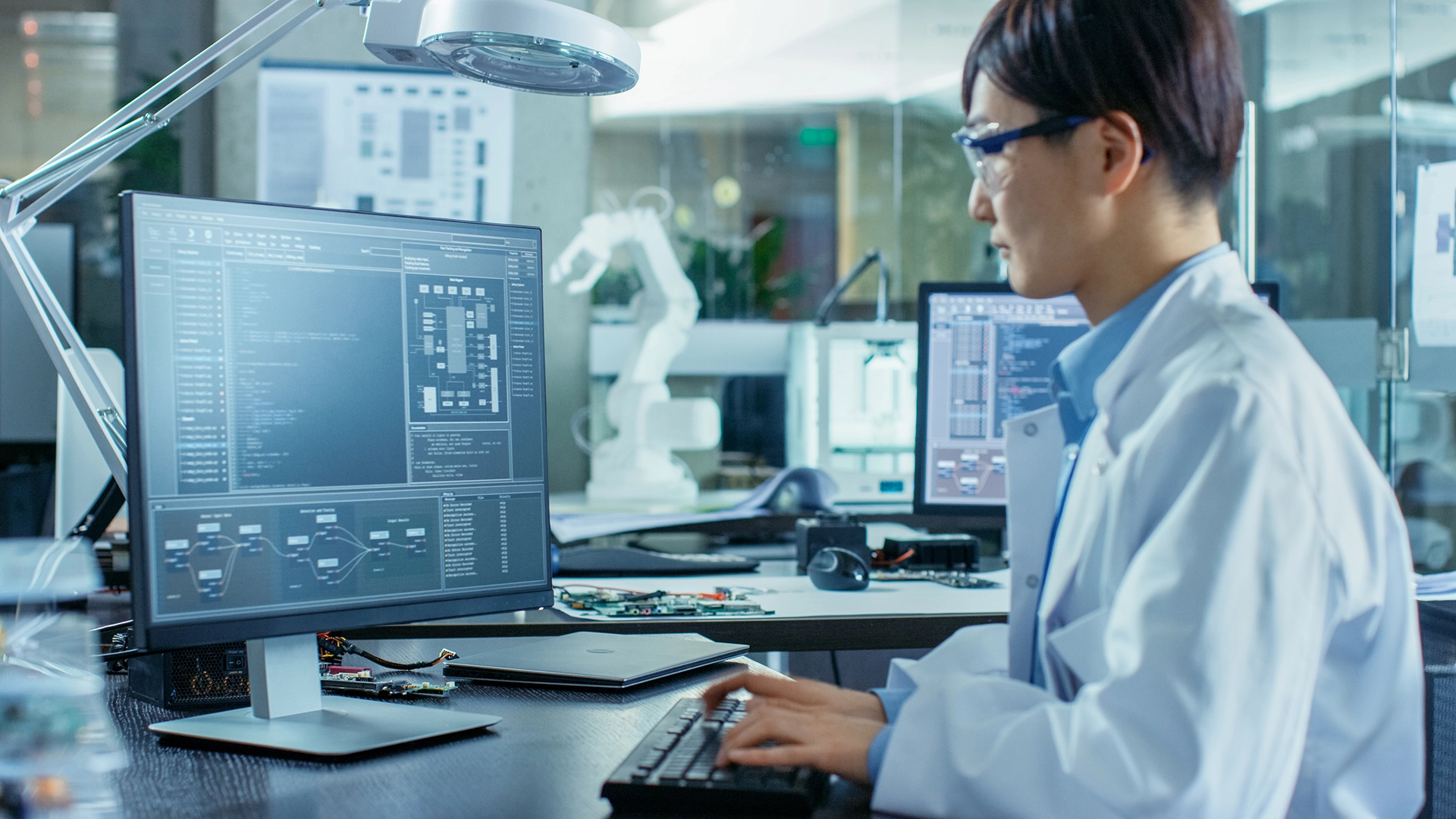
The Manufacturer Can Follow Your Designs
If you provide clear-cut, detailed product designs and the samples don't follow them, this is a red flag that indicates the supplier may not be a good fit for your product. If there is a minor problem with the sample, allow the supplier to make adjustments and send out a new sample. If the sample is completely different from what your designs specify, you'll know it's time to shop for a new supplier.
The Manufacturer Has Quality Control
Even if the supplier follows your specific schematics, a lack of quality control will produce an inferior product. Providing a high-quality sample demonstrates that the supplier has the means to follow quality-control protocol during mass production. We'll talk more about why quality control is important (and how to manage it) later in the article.
Whether Your Product Design Works
This will be particularly important if a supplier is creating a prototype (not just a regular sample) before mass production begins. Even if they follow your designs perfectly, it won't mean much if your prototype doesn't work. The sample may reveal that a different raw material needs to be used in order for the prototype to function, or that your price-point needs to be adjusted to accommodate new design details.
It may also mean that you need to find a supplier that has a stronger specialty in your niche (this is especially true if you know your prototype works but the manufacturer just can't seem to get it right, even after following your specific designs). All of this must be taken into consideration if you are going to build a prototype.
Sourcing Specialists Shine in the Sampling Process
The sample step is paramount to ensuring that you and your supplier are a good fit. You can expect to go through this process several times when you're looking for a supplier for the first time. This is where experienced sourcing agents, like Kanary, offer enormous advantages to the manufacturing process.
For example, the Kanary Team already has an extensive network of established, reputable manufacturers that we can rely on when sourcing your product. This eliminates the tedious back-and-forth nature of refining the product in the sampling process. Eliminating the hassle of the sample step (and finding the right supplier the first time) is one of the strongest advantages Kanary offers.
Quality Control: Boots on the Ground
Once you have an acceptable sample in hand, you'll give the go-ahead for the manufacturer to begin mass production. However, this is not the time to sit back and wait for your order to be completed. Even if a supplier has demonstrated the ability to provide quality control, it doesn't mean they will.
It is common for low-quality suppliers to provide an excellent sample and then cut corners when they begin the larger order. Common corners a supplier may attempt to cut include:
● Supplying low-grade raw materials
● Skipping steps in the assembly process
● Improperly storing and shipping completed products
The only way to guarantee quality control standards and make sure a supplier is held accountable, is to have someone physically present during the manufacturing process. Having someone physically present during this process has enormous benefits, including:
Guaranteed Quality Control
The obvious advantage of having someone physically present is that it guarantees that quality control steps will be followed. The peace of mind that comes from knowing, without doubt, that your products will match the high-quality sample you received, is an enormous benefit.
Rapid Response to Problems
Even if corners aren't being cut, having someone onsite can help navigate sudden problems that require quick decision-making. For example, major equipment failure may drastically change your production timetable and require down to the minute decision making.
Other problems that require quick decision making may include issues with an associated supplier (like a raw material supplier having issues that impact an assembly supplier), problems like civil unrest, or any other sudden social changes. In February 2020 when the COVID-19 pandemic hit China, it crippled the manufacturing industry, and those without feet already on the ground were left in the dark about what to do.
Quickly Answering General Questions
Finally, a manufacturer may need your general input before moving on with production. Having someone onsite, as opposed to relying on communication with someone through e-mails and phone calls at odd hours, is a great benefit. Without this, your production time frame can easily be compromised.
Videos and Photos Help Quality Control
If you absolutely cannot be at the factory site (and are still choosing not to use a sourcing agent), then the next best thing is regular photos and videos. While some suppliers won't show you everything (they'll want to protect their trade secrets), reputable suppliers will still provide videos and photos of finished products along with storage conditions.
Sourcing Agents and Quality Control
This is another area where product sourcing agents, especially Kanary, excel. We have a permanent office in China, and we personally supervise the production of all orders placed through us. Our experienced quality-control experts guarantee that the production process will not cut corners and that your exact specifications are followed.
Time to Ship
Once products are complete, it's time to start the shipping process! You'll want to ask the manufacturer for a record of all products made and how they were packed. This documentation may be required to load products onto your container.
Remember, you should have already ordered your container the moment production began, not once the order is complete.
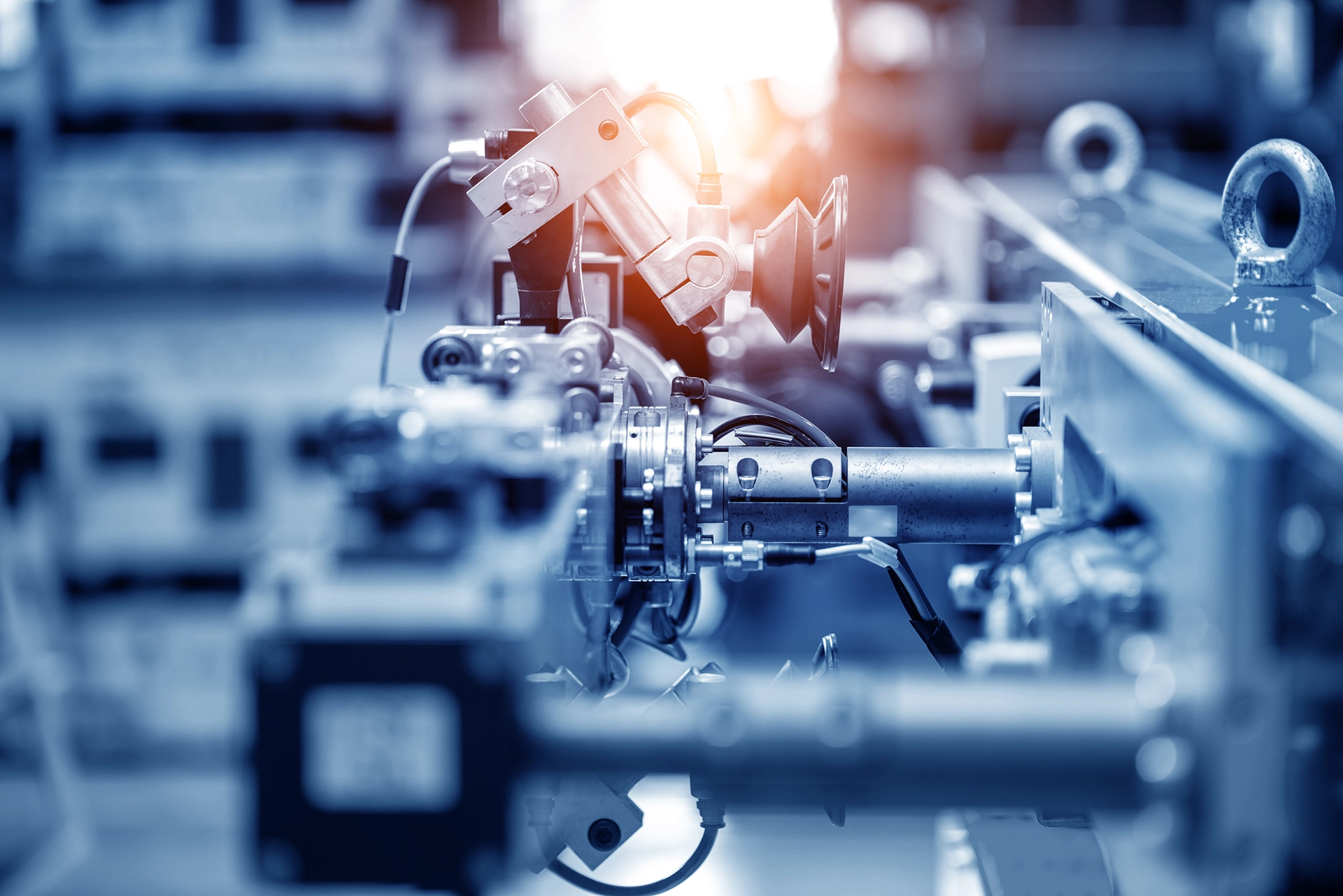
Kanary and China Manufacturing
By now, you can see that manufacturing in China is no small feat. It requires clear communication of designs and expectations, an intensive sampling process, and constant supervision to ensure quality control. If that process sounds overwhelming, consider letting the Kanary Team take the reigns as your sourcing agent!
When it comes to manufacturing your products in China, we offer enormous advantages, including:
● Using our established network of high-quality manufacturers to help you find the ideal supplier without the hassle of trial and error
● Managing the entire sampling process, including managing multiple samples from multiple suppliers and consolidating the shipping to save you money
● Supervising quality control both onsite and from our China offices
● Facilitating clear communication with our bilingual manufacturing experts
If you think that Kanary would benefit your business, reach out to us! We offer a free consultation to discuss what your needs are and whether the Kanary Team would be able to effectively meet those needs.
We look forward to hearing from you!