When sourcing products from China many businesses focus heavily on finding a quality manufacturing partner and the logistics of shipping. A crucial, yet often overlooked, step in the sourcing process is quality control. If you're serious about capitalizing on China manufacturing for your business, you cannot afford to ignore quality control.
Quality control steps will vary depending on the specific product being sourced and the industry you are in. However, the Kanary Team has put together some very important reasons that show why it is a necessity to dedicate a large amount of time and effort focusing on the implementation of quality control measures. We will also give you the best tips on how to put those measures into practice.
If you've been curious about why quality control is an important factor when manufacturing in China, then this article is for you!
Quality Control with Raw Material Suppliers
Making sure your product adheres to strict quality control guidelines begins with the raw materials. If your supplier uses low-quality materials or cuts other corners (like using a lower grade of steel than you requested), you will end up with a low-quality, defective product. This is true even if your assembly supplier is excellent.
Example: Vape Cartridge
As an example of how raw materials can impact quality control, we'll look to a basic vape cartridge. These products depend on the best raw materials available, such as high-quality ceramic for the heating elements and top-grade cotton for the wick. If either of these materials are low quality, no matter how efficiently the final vape cartridge is assembled, the vapor flavor will be negatively impacted.
You also need to make sure the elemental components (like the metal, plastic, and glass that will hold the vape juice) are pure. This will ensure the cartridges do not leak and that the atomizer components do not emit harmful toxins into the vapor. Even parts like the mouthpiece need to be made of plastic that is of food-grade quality (which poor suppliers will try to skip resulting in a defective and possibly harmful product).
All of these factors should be taken into consideration before even considering the quality control steps involved during the assembly phase. If your raw materials are less-than-adequate, your entire product is doomed to fail.
Example: Glass Jars
When it comes to manufacturing a complex product (like a vape cartridge), it’s easy to understand that there will be problems associated with ignoring the quality control steps. However, even simple products can suffer greatly if quality control measures are ignored. Glass jars are a perfect example of what appears to be a simple product that can greatly suffer from lack of quality control.
We help a variety of clients source glass jars from China, and the majority of those clients aren’t selling empty glass jars. Those businesses need glass jars to put different products inside. For example, we have a variety of cannabis growers and dispensaries that put cannabis in glass jars when they sell to the end consumer.
The thickness of those jars is extremely important. Having brittle, light weight jars filled with a product meant for human consumption, is a recipe for disaster. Low-quality suppliers may attempt to sell jars with especially thin glass to save on material costs. This presents huge problems. For starters, many of the jars most likely will not survive shipping (especially if you are using sea freight). For the ones that do, the common breaking of the glass while packaging will be a very real scenario, ruining the product and costing you money. Furthermore, it may have a negative impact on your business reputation, all because you ignored quality control!
Quality Control with Assembly Suppliers
Once you establish that your raw materials are top-grade, you will want to consider how to implement quality control at the manufacturing step with your assembly suppliers. Quality control will be essential in the assembly phase, since this is where product defects most often occur.
Focusing in on quality control during this phase will help to guarantee that your vision for your product is successfully accomplished and that your brand is synonymous with quality. When customers associate your business with consistent, high-quality products, they will become loyal, repeat customers.
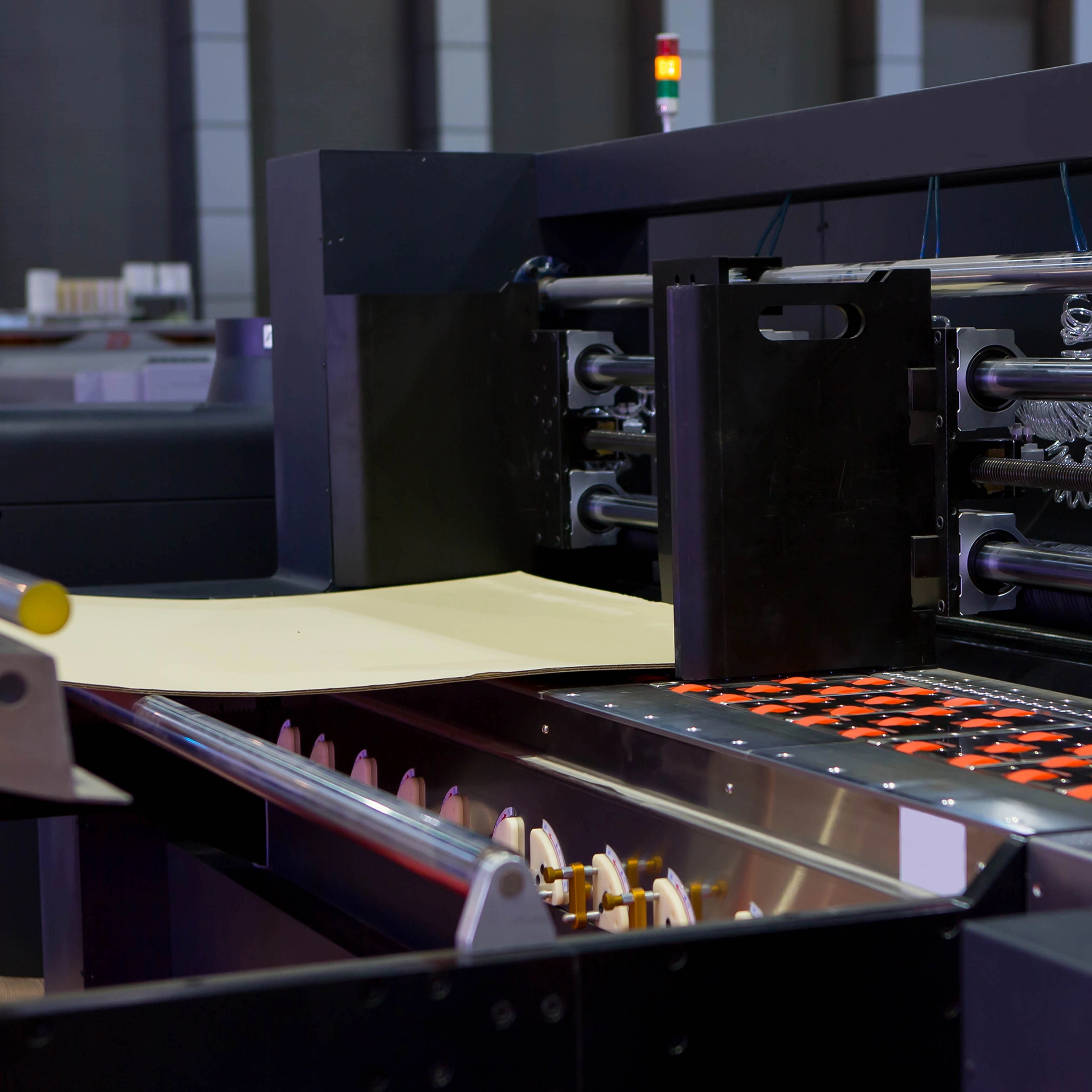
Example: Box Packaging
Box packaging is a great example that has a simple raw materials process and a very complicated assembly process. The only significant quality control step in sourcing the raw material for box packaging are the thickness of the sheets of paperboard. The thickness still needs to be confirmed (which the Kanary Team checks by inspecting a sample) because low-quality suppliers will order thinner paper to save on material costs.
After your assembly supplier has sourced sheets of paperboard, they will begin to look for a printing vendor. Making sure quality control steps are followed here are crucial because your supplier has an incentive to go with the cheapest print shop, while your best interest lies in the highest-quality print shop.
You may think that checking a printed sample will help you avoid suppliers using low-quality print shops, but this just is not the case. The sample you receive will be digitally printed (which means the assembly supplier is not commercially printing your samples). The difference between your digitally printed sample and what the commercial printer ends up producing could have enormous quality differences.
Kanary avoids this issue by partnering with the supplier to choose a print shop that has already produced quality work for us in the past. If you are placing orders on your own, you have to verify that the print shop being used is capable of producing the high-quality finish for the packaging you desire. You will need to check references with other businesses that have used this print shop, or personally inspect the print shop yourself to guarantee quality.
Special Design Effects
If your box packaging is going to have a simple finish, then it will move to the cutting and assembly phase after printing. If the finish is going to be more detailed and you plan on using special design effects (embossing or UV printing), then there will be an additional step in the strategic sourcing process (where you must verify and maintain quality control).
Some assembly manufacturers will ask the print shop to handle the UV printing or embossing in-house. If you or the supplier have a concern with the print shop meeting quality standards, you may decide to outsource the special design effects to another shop.
As you can imagine, making sure that suppliers adhere to quality control steps when embossing or UV printing is a demanding, time-intensive process. This is especially true if you need to ship products to an additional third party in order for the designs to be implemented.
If you are concerned about print shops or suppliers cutting corners with special design effects, then partner with Kanary! We have been sourcing box packaging for clients for more than 10 years and have established fantastic relationships with high-quality print shops and suppliers. We take the guesswork out of choosing a print shop since we already know which ones consistently produce high-quality work.
Cutting
After all designs are printed on your box packaging, the paperboard is returned to the assembly supplier who will begin cutting. This may seem straightforward, but quality control issues are common in the cutting phase too. Low-quality suppliers will cut your boxes improperly, cutting out pieces of words or designs that make the boxes worthless for branded packaging.
If you ordered boxes that are meant to be child-proof, then cutting is an even higher priority in your quality control steps. Boxes that are not properly cut, will not properly fold, which means that they can not be used for products that require child-proof packaging. Again, even if your original sample met your expectations, this is not a guarantee that the mass-production phase will meet your quality standards.
Improper cutting is a quality problem that you would not see until after the boxes are shipped to you (a supplier will not send you a sample of a cut box, unless you specifically request and pay for it). The only way to guarantee this aspect of quality control is to have someone physically present in the factory to check boxes as they are cut. If you partner with Kanary, you are guaranteed to have someone physically present to check boxes during the cutting phase to eliminate the chance of faulty packaging.
Packing for Shipment
Finally, once the boxes have been printed and cut, you will need to make sure that your supplier appropriately prepares them for shipment. The supplier needs to use the correct cartons for packing, since cheap cartons will not protect the edges of your boxes, resulting in bent or broken edges.
Palletization also happens in this step, and if you allow the supplier to skip it, you will end up paying hundreds, if not thousands, of dollars in added costs. First, if you are using warehouse storage (something you will do if you are taking advantage of consolidated shipping), palletized boxes can be quickly and easily moved within the warehouse. If the boxes are loosely stacked, moving them will require manual labor, which is an extra cost you pay for.
Palletization protects your boxes once they are loaded onto the container, as it prevents movement while the vessel sails. Having your boxes properly palletized will expedite the unloading process when it reaches its destination port. However, if you just have loose boxes in the container, it will take an extended period to unload them from the container and onto the trucks of your carrier partner.
Your carrier drivers have two hours to load your products onto the truck. If you did not do you due diligence in making sure your products were palletized, and it takes the carrier partner more than two hours to load, you are looking at $100 an hour extra to just get your boxes onto the truck.1
Without following quality controls steps in the packing phase, you will end up paying huge extra costs for products that are bent and damaged. This phase is especially important for box packaging, which is why the Kanary Team takes extra care to ensure that box packaging is properly packed for shipment.
Example: Rotary Pouch Bagging Machine
As our second example, we will speak about machinery. If your business sells products in branded, plastic bags, a high-quality rotary pouch bagging machine is a necessity (especially when you are attempting to scale production). Being able to prepare packaging for retail sales quickly and reliably can make or break your business.
We have significant experience helping clients successfully source rotary pouch bagging machines from China. We take pride in sourcing these machines particularly because these machines are very expensive and often extremely intimidating from a purchasing standpoint. Without the proper knowledge and experience, these types of purchases will go very wrong and end up as a huge, burdensome expense. We have seen many suppliers offer too-good-to-be-true prices on these machines, and the corners they cut can cause unrecoverable financial losses.
The most common problem we see is when suppliers attempt to swap out reliable, high-end electrical components for cheaper, unreliable counterparts. We always make sure that the PLC system of these machines are specifically branded or sourced from reliable companies in Japan.
In order to offer a lower price, suppliers may attempt to offer a bagging machine with a Chinese-made PLC (or programmable logic controller, which is the component that allows you to configure and run the machine). While you can source a variety of excellent products from China, the country simply cannot compete with PLCs made in Germany or Japan. Without proper quality control measures, you may end up with an inefficient machine because of a low-grade, faulty PLC.
The result? You will have a fantastic looking bagging machine that can’t function until costly repairs are made. This can crush your production line, ruin your scaling plans, and add an unrecoverable cost that would have been avoided by supervising and implementing quality control measures.
Quality Control in Packing and Shipping
Lastly, but just as important, a final step to assuring quality control in the assembly process is to make sure that finished products are correctly packaged. Using the vape cartridge example, it means they should be packed in egg cartons (or something with similar durability) to protect the more fragile components from cracking and leaking during shipment. A low-quality supplier may overpack, which could lead to damaged goods. More often than not, this goes unrealized until the products are delivered. A low-quality supplier may also under-pack, using more cartons than necessary, unnecessarily increasing your shipping costs.
Even after products are carefully made and appropriately packed for shipping, quality control implementation is still not over. Making sure finished products are correctly loaded onto containers is especially important. The hasty, unorganized loading of finished products onto a container will almost always result in damaged goods or inaccurate inventory upon the arrival at the final destination.
For example, let’s say you are shipping flat boxes that require assembly once delivered. Careless packing can equate to bent or ripped edges caused by avoidable movement during transit if the container was loaded right. Upon delivery, a certain percentage of those boxes will be rendered useless, and you will be out of luck. Again, you won't have any idea that your products have been damaged until after you receive them.
If goods aren't loaded or palletized correctly, it can lead to an unbalanced shipping container. This can and will net you enormous fines. An unbalanced shipping container means that your receiving trucking company is unable to deliver your container until the container is balanced. This means you will be legally required to pay a company to unpack and rebalance your container, and the fee they charge is at their discretion. This can delay the date you are supposed to receive the container by days or weeks, and the massive fines are unavoidable.
Making sure quality control measures are followed for shipping not only protects products against unnecessary damage, but it also will help to ensure you stick to your production time frame and avoid significant fines.
How to Implement Quality Control in Manufacturing and Shipping
The only way to guarantee that quality control measures are followed during shipping and manufacturing processes is to have someone physically present supervising production and logistics. They not only need to be supervising the manufacturing and packing process, but they also need to be present at the port of origin for the loading of the container.
Having someone present at the port of origin will allow you to control how quickly and correctly products are loaded onto the shipping containers. It is also a good idea to have a trusted company at the port of destination (port of discharge). This will allow you to control the final shipping of your products from the port to the end destination.
Implementing quality control steps during manufacturing and shipping requires having a dedicated person (or a dedicated team) that can spend extended time in China. They will need to have a deep understanding of what quality control entails, supervise manufacturing, and identify red flags in the raw material, assembly, and shipping phases.
Of course, this means that this dedicated person (or team) will also need to be available in the destination country (or at least have a competent, trusted counterpart available) to guide the unloading and final shipment process.
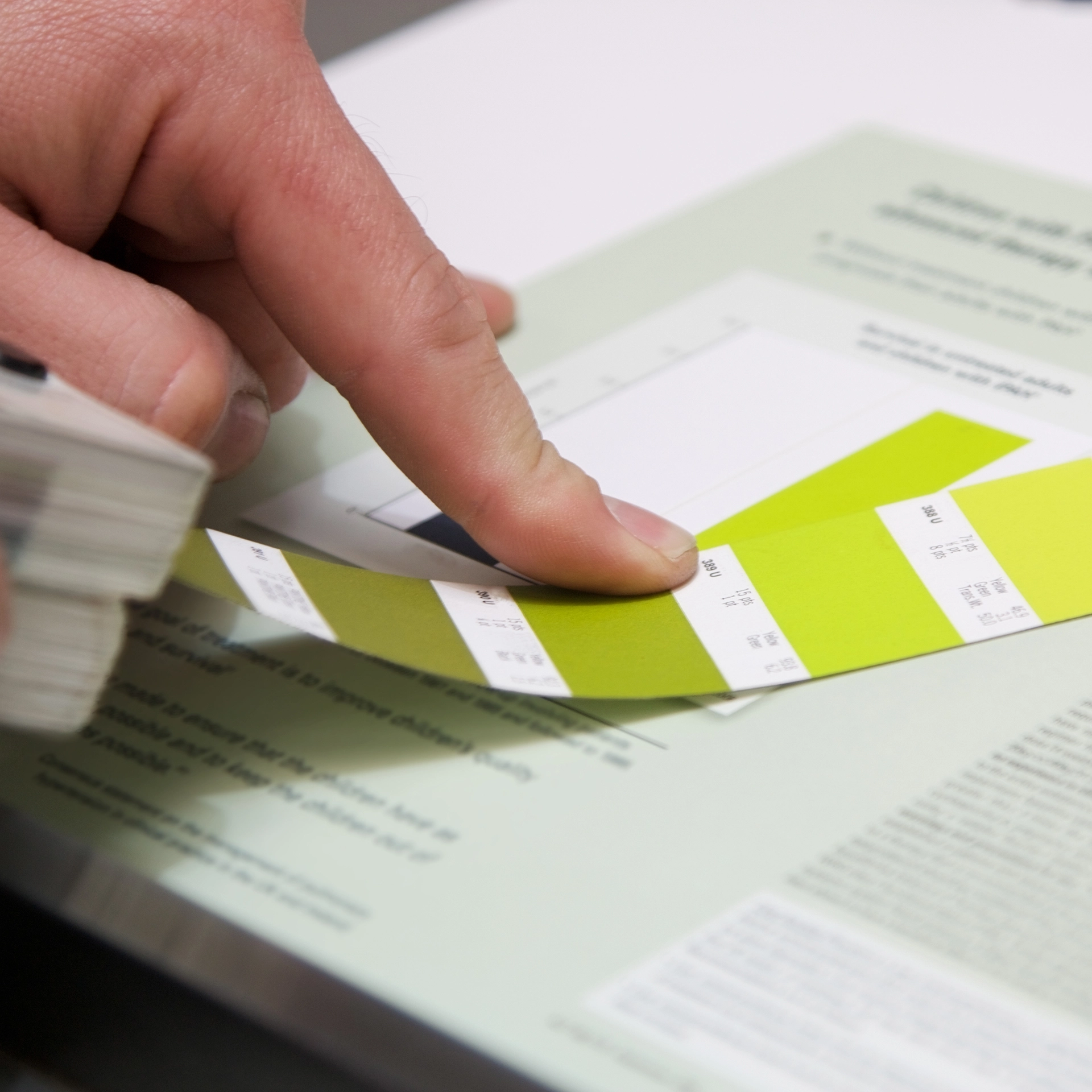
Kanary Team Sourcing Specialists: Quality Control
For most businesses, the cost of creating a position or dedicated team to supervise quality control is simply not feasible. If you value quality control but feel that your business would be unable to guarantee its execution, then consider partnering with Kanary as your sourcing specialist.
Quality control is among the variety of advantages that we offer businesses looking to China for their manufacturing needs. We guarantee the best quality by having our team onsite, in China, to supervise the manufacturing, packing, and shipping of your products, as well as onsite, in the United States, to help receive, deliver, and provide support after delivery.
Our team members have spent decades perfecting the quality control steps during manufacturing and shipping processes, specifically in China. Partnering with us means you get the advantage of an in-person guarantee that your quality control standards are met.
If you feel this may be a solution you have been looking for, reach out to us! We offer free consultations and only partner with businesses that we believe we can offer genuine value to. We look forward to hearing from you soon!